Krasnoyarsk scientists and manufacturers have launched the production of nanomodified paint
20 March 2023 г. FRC KSC SB RAS
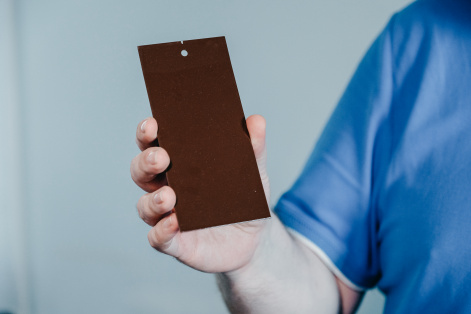
The paint was developed according to the original technology of scientists of FRC KSC SB RAS. It consists of aluminum oxide nanofibers. Such an additive improves the operational properties of the paint, in particular, it makes the coating twice as strong, increases elasticity and corrosion resistance by more than 40%. As a result, such powder paints can replace imported analogues.
Any conductive material can be coated with such paint, for example, the housings of refrigerators and other devices. The anti-corrosion qualities of the paint will be important for ship rigging in order to protect it from the aggressive effects of the sun, water and salt. They can also be used to protect other equipment from corrosive loads, such as road signs and transformer boxes, servers and relay equipment.
Mikhail Simunin, Candidate of Technical Sciences, Leading Engineer at the Department of Molecular Electronics of FRC KSC SB RAS, comments on the development and implementation of paint in production: “We have finally launched the production of nanocomposite paint on an industrial scale. There is an interesting set of circumstances: exactly four years ago we completed the development of a technology for the production of aluminum oxide nanofibers, which is distinguished by increased reproducibility and reduced synthesis costs. And now, four years later, around the same day, we sold the first large batch of our first market product based on these nanofibers.
All this time we have been studying the properties of nanofibers and methods of their introduction into other materials. The lab has been developing methods for surface treatment of nanofibers so that they can be embedded in a polymer and chemically bonded to macromolecules. Our industrial partners helped us a lot. For example, the general director of the production of ventilated facades in Krasnoyarsk, being an enthusiast in his field, became interested in our materials and suggested adding them to the polymer material of his composite panels. For this, a well-known industrial extrusion method was used. The result showed an increase in the tensile strength of the polymer by almost three times. However, this did not give a dramatic change in the consumer properties of composite panels, since another type of strength is important for this - bending strength. We realized two main things: the extrusion method is good for us and that the aluminum oxide nanofibers increase the cohesive energy of the polymer, in other words, it becomes more difficult to break it.
Near Krasnoyarsk, in the town Zheleznogorsk, there is a production of powder paint and its general director became interested in our additive, since it is intended for coatings whose properties such as adhesion and cohesion play an important role in consumer characteristics. Moreover, new environmentally friendly coatings crosslinked with amine hardeners were mastered at the production site. The strength of such coatings is evaluated by throwing a striker weighing 1 kg from a given height. Without an additive, the coating is destroyed when the striker hits from a height of 50 cm, and with an additive it does not collapse when it is hit from a height of 60 cm. On the device, 60 cm is the maximum scale. Therefore, the margin of safety of the coating modified with our nanofibers remained a mystery to us. We also showed an increase in the corrosion resistance of the coating and understood the perspectives of our nanocomposite paint. It turned out that the corrosion resistance increased from 5 to 8-12 years! That is enough for the market.
Before manufacturing our products, we bought a new strength measuring device with a scale of up to 100 cm in order to correctly assess the increase in the coating strength, but here a surprise awaited us - the coating withstood the impact of the striker from a height of 100 cm. Thus, even the expanded scale of the device for assessing strength was not enough. But now we can talk about an increase in strength not by 20-25%, but about a double increase.
The manufactured industrial batch of paint will be used to cover profiles in the cooling tower, where the environment is humid and aggressive. There we rely on the long service life of the coating and feedback from the customer based on the results of operation in real conditions.
Share: