Elastic electroconducting films have been created in Russia
9 October 2019 г. FRC KSC SB RAS
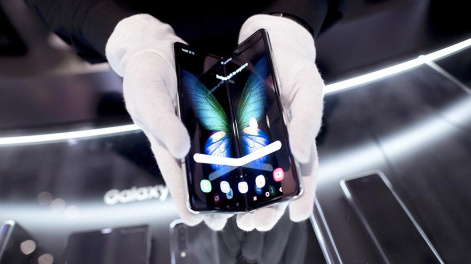
Battle for the radius
Indium tin oxide is used as the conductive base in the screens of most modern mobile phones, but its plasticity is limited by a large bend radius of about 3 cm. To solve the problem, Russian scientists created a material with a bend radius of 2 mm.
New films will make flexible mobile phones as thin as possible, distinguishing them from the existing ones. For example, the thickness of the flexible smartphone Samsung Galaxy Fold is 17 mm, and its Chinese competitor Huawei Mate X is slimmer by as much as 6 mm. However, it does not reach the dimensions of classic devices - in particular, the thickness of the recently introduced iPhone 11 is only 8.1 mm. In fact, innovative smartphones are two classic cases combined in a single design. New materials should reduce their dimensions due to a simpler screen design, which implies fewer functional layers. In addition, screens created on the basis of Russian films will have lower reflectivity, to make the use of phones more convenient in sunny weather.
Another advantage of the new films is their ability to repeatedly stretch up to 100% while maintaining operability, which is achieved owing to a special method for production and deposition of carbon nanotubes on a polymer base made of polydimethylsiloxane.
“To create the material, we use a chemical reactor, and a stream of iron nanoparticles and a carbon-containing gas (for example, methane) is fed into its tube, decomposing at a high temperature (about 1000 ° C), and turning into single-walled carbon nanotubes,” explains the head of the laboratory of Nanomaterials at the Skolkovo Institute of Science and Technology, Professor of RAS, Albert Nasibulin. - Then, the resulting aerosol nanotubes from the reactor fall onto a special highly-porous filter for its surface to be covered with a transparent layer of randomly oriented carbon nanotubes with a controlled thickness, which can range from units to hundreds of nanometers.
At the final stage, the scientists transfer the resulting structures to the polymer film mechanically, pressing a filter to it. As a result, a layer is formed, which mainly consists of individual nanotubes, while using alternative methods of production, specialists obtain entangled particles with other properties.
“Before applying the nanomaterial to the polymer, the latter is pre-stretched,” says the head of the Department of Radio Engineering and Electrodynamics of the N.G. Chernyshevsky Saratov State University, Olga Glukhova. - After the nanotubes cover it, the edges of the film are released, and it restores its original size. Thanks to this, it is possible to achieve a wavy structure of the material, which ensures its stretching without changing its electrical conductivity.
Iron touch
If two components of a film are tied together without preliminary stretching, then as the size changes, its resistance will change (due to a change in the thickness of the nanotube layer). This property can be used in creating medical sensors for making electrocardiograms as well as for monitoring heart rate and respiration.
“In this case, readings are taken more qualitatively than in the case of using conventional metallized electrodes, since the noises arising upon their use are eliminated,” says Albert Nasibulin. - Currently, we have successfully confirmed this fact on one of the medical devices.
In addition, we are planning to create flexible touch and pressure sensors on the basis of flexible films, which will allow “covering” robotic arms - this will enable them to have high tactile sensitivity and to perform finer work.
However, there are critical estimates of the development.
“Scientists use the original technology for the synthesis of carbon nanotubes, and the films obtained have the best parameters in their class,” says Anton Voronin, an employee of the FRC “Krasnoyarsk Science Center” SB RAS. “However, if to compare this product with silver and copper nanofibers, the latter have lower electrical resistance while having the same flexibility, which makes them more suitable for creating new-type screens.
According to the expert, the greatest benefit from applying the films can be achieved in creating pressure sensors.
For a wide practical implementation of the development in the future, it will be necessary to create demand from electronics manufacturers for the mass production of devices with elastic screens. Before this, scientists still have time to improve the characteristics of the material - in particular, to reduce its resistance, which is still slightly higher than that of its analog made of indium tin oxide.
The market price of the new film made of carbon nanotubes and polymer material is expected to be comparable with the price for indium tin oxide, amounting to about $ 20-30 per square meter.
Source: Izvestia
Share: